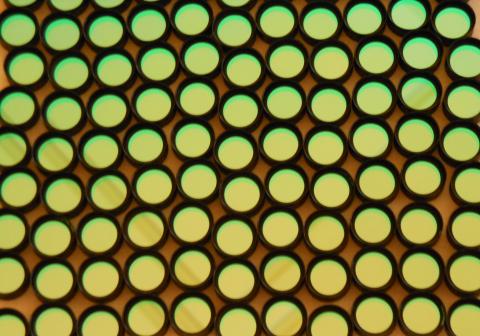
Omega Optical employs the widest range of coating technologies in the optical thin film filter industry. In addition to our high capacity, state-of-the-art Helios Plasma Assisted Reactive Magnetron Sputtering (PARMS) systems, we’ve retained the ability to produce filters made with traditional inorganic compounds, typically zinc sulfide and cryolite. Each technology has its own strengths.
Many inorganic compounds can be evaporated with relatively simple vacuum systems, and condense into uniform films without the assistance of plasma or high energy ion beams. Consequently, filters fabricated this way, often referred to as soft or protected filters, have a substantial cost advantage over filters manufactured using PARMS. A typical PARMS production run will cost between $10,000 and $30,000, while the cost of a soft coating production lot is around $2,000. While this cost differential is offset by the much larger capacity of the Helios systems, the protected film approach offers a cost effective route for small volume production, particularly during early development stages where specific spectral requirements are being established.
Soft coatings must be protected with a cover plate. Having the optical film embedded within the filter structure has its plusses and minuses. Since the film is beneath a layer of glass and protected from the environment, it is in no danger of damage. In fact, in the early days, Omega was involved in several space-missions that employed these types of filters, including the Halley's Comet fly-by in 1984. On the other hand, the uncoated glass surfaces of these assemblies result in a 3.5% transmission loss per side because of the inherent reflectivity of glass. In particularly humid environments, the optical epoxy bonding the cover plate can absorb moisture resulting in a loss of transmission. For this reason, the life time of protected filters is usually considered to be less than 10 years.
There are many advantages to PARMS manufactured filters. The coatings are extremely hard, allowing the coatings to be exposed to the environment. This durability, combined with the absence of an epoxy layer, results in an expected lifetime in excess of 10 years.
The sophisticated monitoring of modern PARMS systems allows a level of coating design complexity not possible with protected filters. The manual layer terminations of the latter limit executable designs to quarter wave based options. PARMS coatings have no such limit, allowing the execution of a much wider range of designs, including flat-top narrow bandpass filters and multiband designs. Also, because of their greater layer termination accuracy, much thicker coatings are possible with PARMS coatings. Spectral performance that would require 3 or 4 separate thin films with a protected filter approach can be achieved with 1 or 2 coatings using PARMS. This means that the overall filter assembly thickness can be significantly less. Protected filters need to be around 5 mm thick, while the typical PARMS filter is ~1 mm thick and can be much less. Other benefits of the PARMS monitoring system are greater lot-to-lot repeatability and higher overall transmission. While a typical protected filter will have around 80% peak transmission, PARMS filters will routinely exhibit greater than 95% transmission, with deeper out-of-band blocking and steeper edges.
Take advantage of Omega's flexibility and 50+ years of innovation in coating technology when considering your next filter purchase. We are happy to walk you through the design choices and help find the perfect solution for your application and price-point.