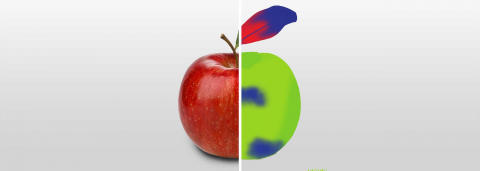
We are currently living through a major shift in industrial thinking. This is mainly focussed on the digitization of manufacturing processes, which is – in turn – based on greater automation and interconnectivity. You might have heard of Industry 4.0. The catch-all term used to describe a revolutionary paradigm shift affecting virtually every facet of industrial processing. At Omega Optical, we’ve witnessed this continued change through our industrial optical filters business.
What is Industry 4.0 & Why Do Industrial Optical Filters Matter?
Industry 4.0 started with the computerization of workflows in the era of digitization. This era of digitalization, which resulted in the development of Industry 4.0, is loosely defined as the period between 1969 – 2012; also known as the Third Industrial Revolution or Industry 3.0. But our ability to design intuitive mesh networks of complementary devices that communicate their own intrinsic, vital pieces of data now goes far beyond the capabilities of the late 20th Century.
Today, process engineers can remotely monitor critical process metrics using high-performance sensors that continuously relay data to central processing hubs. There’s no limit to the number of parameters that can be measured using these discrete integrated elements. This is where industrial optical filters come into play.
Industrial Optical Filters: Harnessing Light in Process Control
Manufacturers routinely harness light to control and/or perform various critical processes in their industrial workflows. Photolithography and laser materials processing are among the most common – and lucrative – areas where industrial optics are deployed. But precision sensing elements and machine vision systems play crucial roles in the new process control landscape of Industry 4.0. Let’s explore one example.
Semiconductors are among the most advanced materials of the modern age. They form the backbone of practically all modern electronic devices, from smartphones to photovoltaic solar cells. It’s a small wonder that the global semicon market is currently valued in excess of $481 billion. But manufacturing electronic wafers derived from semiconducting ingots is complicated, mandating next-generation process control procedures.
A Case Study: Inspecting Semiconductors
To fabricate an electronic substrate, you first need to grow single-crystal ingots at high-temperatures in controlled atmospheres. A wafer of around 200 – 300 millimetres must then be extracted from the ingot and planarized for absolute topographical uniformity. We are approaching the need for practically zero tolerance with key surface features on semiconducting wafers reaching lower than 100 nanometres (nm). Few inspection probes can provide that level of assurance.
Ultraviolet (UV) laser light is commonly used for semiconductor inspection; hence the need for precision-made industrial optical filters. Working in the UV region has proven difficult for industrial optical filter manufacturers in the past, as most materials absorb light of wavelengths below 400 nm. Plus, standard filters cannot provide the level of blocking width required when dealing with sub-400 nm wavelengths. There are various methods for both enhancing the performance of industrial optical filters for deep UV laser light and integrating performance notch or bandpass filters in wafer inspection systems.
Looking for UV filters?
Cameras with integrated DUV detection are only becoming more crucial to wafer inspection as manufacturers increasingly push towards greater electronic density.
Industrial Optical Filters from Omega Optical
Clearly, the scope of industrial process monitoring is far too big for us to cover in a single article. This was merely intended to offer a brief insight into the importance of industrial optical filters in the changing world of Industry 4.0. Want to know more? contact a member of the Omega Optical team today and we would be happy to talk you through the various process control applications that we can help with using our tailor-made optical filters.