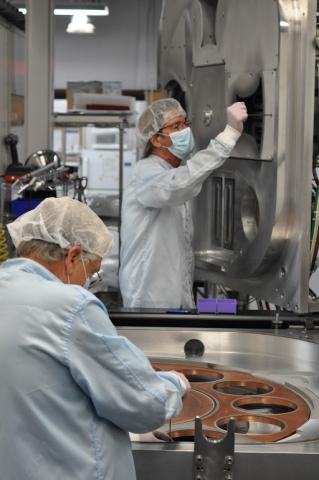
“Quality is never an accident; it is always the result of high intention, sincere effort, intelligent direction and skillful execution; it represents the wise choice of many alternatives.” ~William A. Foster
Quality is the key to successful filters and optical systems. At Omega Optical, we want filters that outlast, outperform, and inspire - and are grateful to have a quality assurance team that has taken this to heart. Today, we are excited to share with you an insight into our manufacturing processes and give a quick shoutout to the staff that makes this whole thing possible!
Quality Assurance vs Quality Contol
Quality assurance (QA) and quality control (QC) are two independent but equally vital components of the optics manufacturing process. While similar, the two function quite differently. QA involves maintaining a quality system that keeps track of regulatory reporting, performing statistical process analysis, and maintaining production records, as well as document control. QC specifically refers to the actual inspection of components and products on the shop floor. Omega Optical, LLC maintains both QA and QC and proudly serves our customers under a certified ISO 9001-2015 Quality Management System.
Preparing Initial Materials
The typical flow of manufacturing starts with gathering the materials needed for manufacturing. Such materials include raw (unpolished or uncoated) glass, filter rings (to be sent out or being returned from anodization), and pre-configured substrates ordered to a specific customer need. Consulting the Tech Sheet and Assessing Materials First, the QA tech will consult the relevant spec sheet or mechanical drawing and compare this with the actual measurements of the materials being inspected. After a visual inspection for defects, the critical dimensions are called out by the drawing or Manufacturing Control Sheet and are recorded on the Incoming Inspection Report. Engineering is consulted in the case of nonconforming material and a determination is made as to accept a part as-is, rework it, or return the part to the vendor.
Measuring with NIST Standard Devices
The measurements are made with devices calibrated to standards aligned with the National Institute of Standards and Technology (NIST). QA is also responsible for maintaining and certifying calibrations on all measurement tools used in production or inspections. Traceable devices used are digital calipers, Unitron Toolmaker’s Microscope, and the Nikon V12-B Optical Comparator.
Polishing to Your Specifications
The purchased glass substrates will then be sent to our Grind and Polish department to be polished to the precise specified thickness. We primarily use high-volume Speedfam grinders and Hoffmann polishers. The parts are then checked for thickness using a digital micrometer and placed under a high-intensity light for Scratch/Dig per MIL-PRF 13830. At this point, polished plates are checked with a Twyman-Greene BAT Interferometer to ensure the substrates meet Transmitted WaveFront Distortion (TWD) specifications. Critical specifications are recorded and the appropriate sign-offs are added to the Route Tag.
Determining Spectral Performance and Configuring
After the glass substrates are coated, the plates are sent to Spectroscopy, where they are measured for spectral performance on a proprietary Auto Spectro System. This device maps the plates and translates the location of the spectrally conforming parts into G-Code, which can be read by the CNC machines in the Configuring department. This ensures that only the parts that meet spectral specifications are cut to the final dimensions of the configured part. This information is only sent after the Spectroscopist records the spectral data and signs off on the product Route Sheet.
Cleaning and Inspecting
After the parts are configured to their final cut size, they are cleaned and inspected for final dimensions and Scratch/Dig specification requirements. The configuring technician will then record the final dimensions of the configured parts on the Route Tag and sign off that the operation is complete.
Final Assembly
The filters are now moved to the Final Assembly department, where several operations are performed and recorded on the route tag. The parts are re-inspected and given an edge treatment of either optical quality paint or assembled into a mounting ring which has been laser marked with the type of filter and a batch number that corresponds to the route tag. Each of these operations is then recorded and signed off on the route tag as complete. The parts are then measured for final dimensions, which are recorded and signed off as meeting specified tolerance. Filters are then given a final cleaning and cosmetic inspection before being packaged.
Quality Assurance Final Inspection
The completed filters have now reached the final step in the production process; Quality Assurance Final Inspection. The QA technician compares the route tag to the manufacturing control sheet to ensure all required operations are complete and have the proper sign-offs. Documentation requirements are then checked and verified to be conforming to the customer’s requirements. These may include transmission curves, optical density curves, interferograms, and regulatory compliance statements such as reach/ROHS, certificates of conformance, and any additional documentation the customer has requested. Once these requirements have been verified, the QA technician signs off on the route tag and closes out the shop order as complete.
Shipping
The filters are then moved to shipping, where they are given a final count, packaged, and shipped off to the customer. Production records, including the accompanying route tag, are then digitally scanned for document retention. As you can see, Quality Assurance is so much more than the itchy tag you find in your garment that says “Inspected by Number 6 “. This process is dutifully carried out by employees who are highly trained and motivated. Every step comes together to create a filter that boasts the utmost quality.
Recognizing our Outstanding Staff
We want to quickly thank the members of our Quality Assurance Team; Patrick Morrissey, Doris Winslow, Karl Isselhardt, and Paul Jensen. The work you do is the backbone of our company and our products. We do not know what we would do without each and every one of you. Thank you for your dedication, diligence, and enthusiasm!
Have any questions about our quality standards or processes? Contact a member of our sales staff today.